During the National Day and Mid-Autumn Festival holidays, the first batch of mushroom-sorting robots in China were deployed to work. These advanced machines boast a recognition accuracy rate of 99.7%, surpassing human performance by over 10%. Their sorting speed is more than double that of manual labor, and they can identify a mushroom in just 0.8 seconds. Not only do they operate continuously for 24 hours, but they also help reduce secondary pollution caused by manual sorting.
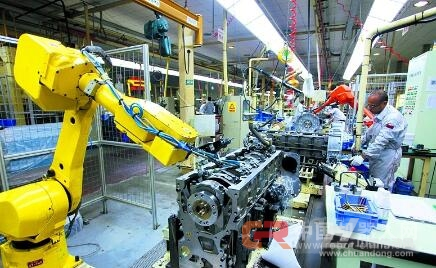
The documentary series "Glorious China," specifically its second episode titled "Innovative Vitality," has received widespread praise. The film highlights a group of dedicated "little yellow workers" — intelligent sorting robots operating in the largest smart sorting facility in China’s express delivery industry. These robots can perform calculations in five minutes that would take one day at Beijing’s busiest airport. They have been celebrated as a remarkable example of Chinese technological advancement.
It's clear that intelligent robots are becoming an essential part of everyday life. China's smart manufacturing sector has undergone significant transformations, reshaping the global landscape. According to a report published by Forbes on October 4th, titled "How China Catches Up with U.S. Uncertainty in the Future," China has rapidly risen to become the second-largest R&D spender globally, accounting for 20% of total global R&D investment. This growth has put pressure on the U.S.'s long-standing dominance in science and technology.
Qu Daokui, chairman of the China Robotics Industry Alliance, has emphasized the need for the robot industry — a crucial component of "Made in China 2025" — to avoid repeating the mistakes of the automotive sector. While China became the world’s largest robot market in 2014, the fast-growing market could either be a golden opportunity or a potential trap. As "Made in China 2025" progresses, the complexity of high-tech products increases, making standardization a critical challenge. In addition to improving product quality, China must also focus on unifying industry standards.
The "Guidelines for the Construction of National Smart Manufacturing Standards System (2015 Edition)" issued by the Ministry of Industry and Information Technology and the National Standards Commission in 2015 aimed to establish a smart manufacturing standard system by 2017. By 2017, the guidelines were revised and improved, strengthening coordination in standardization efforts. The goal was to integrate smart manufacturing standards into the broader industrial framework, with government support for enterprises to develop industry standards.
"Made in China 2025" is often compared to Germany’s Industry 4.0, both representing the future of global manufacturing. Industry 4.0 emphasizes the seamless integration of industrial and information technologies. Germany's strategy prioritizes eight key areas, with standardization and reference frameworks ranking highest. German companies collaborate under a unified standard system, creating a strong ecosystem that supports continuous industrial growth.
In Germany, even elementary schools and archives follow strict standards, such as standardized paper hole punching, ensuring documents remain aligned regardless of orientation. These meticulous standards, enforced by the German Institute of Standardization (DIN), have contributed significantly to the country’s industrial success.
Smart manufacturing is now the new frontier in global production. While international standards are typically developed through three main methods, many aspects of smart manufacturing remain uncovered. Countries must adapt their standards to meet global demands.
As a leading manufacturing nation, Germany excels in industrial technology and has a history of exporting standards. China should learn from Germany’s rigorous approach, aiming to unify its own manufacturing standards under "Made in China 2025." At the same time, it should strive to contribute to the development of international standards, ensuring its place in the evolving global manufacturing landscape.
Digital Printing Membrane Switch
Digital Printing Membrane Switch,Embossed Tactile Membrane Switch,Membrane Switch Panel,Membrane Tactile Keypad
CIXI MEMBRANE SWITCH FACTORY , https://www.cnjunma.com