Motion detector
Displacement sensor, also known as linear sensor, is a linear device belonging to metal induction. The function of the sensor is to convert various measured physical quantities into electricity. The displacement is the amount related to the movement of the position of the object during the movement, and the range of measurement of the displacement is quite extensive. Small displacements are usually detected by strain gauge, inductive, differential transformer, eddy current, and Hall sensors. Large displacements are commonly measured by sensing technologies such as inductosyn, grating, capacitive grid, and magnetic grid. Wherein the grating sensor having an easy due to digital, high accuracy (up to the highest resolution nanometer), anti-interference ability, without human error in reading, easy to install, and reliable, in the machine, the detector forms and other industries It is getting more and more widely used.
Classification and principle of displacement sensors
According to the working principle:
Potentiometer displacement sensor
It converts the mechanical displacement into a resistive or voltage output that is linear or arbitrary as a function of the potentiometer element. Both the ordinary linear potentiometer and the circular potentiometer can be used as linear displacement and angular displacement sensors, respectively. However, a potentiometer designed to achieve the purpose of measuring displacement requires a certain relationship between the change in displacement and the change in resistance. The movable brush of the potentiometer type displacement sensor is connected to the object to be measured.
The displacement of the object causes a change in the resistance of the mobile end of the potentiometer. The amount of change in resistance reflects the magnitude of the displacement, and the increase or decrease in the resistance indicates the direction of the displacement. A power supply voltage is typically applied to the potentiometer to convert the change in resistance to a voltage output. The wirewound potentiometer changes its resistance with a åŒ resistance as a step when its brush moves, and its output characteristics are also stepped. If such a displacement sensor is used as a displacement feedback element in a servo system, an excessive step voltage will cause the system to oscillate. Therefore, the resistance value of each turn should be minimized in the fabrication of the potentiometer. Another major drawback of potentiometer sensors is their tendency to wear. Its advantages are: simple structure, large output signal, convenient use and low price.
Magnetostrictive displacement sensor
The magnetostrictive displacement sensor measures the actual displacement value of the detected product by accurately detecting the absolute position of the movable magnetic ring by internal non-contact measurement and control technology.
The magnetostrictive principle is used to accurately measure the position by generating a strain pulse signal by intersecting two different magnetic fields. The measuring element is a waveguide, and the sensitive elements in the waveguide are made of a special magnetostrictive material. The measurement process is to generate a current pulse from the sensor's electronics chamber that is transmitted within the waveguide to create a circumferential magnetic field outside the waveguide that intersects the magnetic field generated by the moving magnetic ring that is placed over the waveguide as a positional change. At the time of the magnetostriction, a strain mechanical wave pulse signal is generated in the waveguide, and the strained mechanical wave pulse signal is transmitted at a fixed sound speed and is quickly detected by the electronic chamber.
The transmission time of the strained mechanical wave pulse signal in the waveguide is proportional to the distance between the movable magnetic ring and the electron chamber, and by measuring the time, the distance can be determined with high accuracy. Since the output signal is a true absolute value, rather than a proportional or amplified signal, there is no signal drift or variable value, and there is no need to periodically re-mark.
The magnetostrictive displacement sensor is a high-precision, long-stroke absolute position measurement displacement sensor manufactured according to the principle of magnetostriction. It adopts the internal non-contact measurement method. Since the movable magnetic ring for measurement and the sensor itself are not in direct contact and are not rubbed or worn, they have long service life, strong environmental adaptability, high reliability and good safety. It is easy to automate the system and work normally even in harsh industrial environments (such as oily, dusty or other contaminated areas). The sensor uses high-tech materials and advanced electronic processing technology, so it can be used in high temperature, high pressure and high oscillation environment. The sensor output signal is an absolute displacement value. Even if the power is interrupted or reconnected, the data will not be lost, and there is no need to reset to zero. Since the sensitive components are non-contact, even if the detection is repeated, no damage will be caused to the sensor, which can greatly improve the reliability and service life of the detection. The stroke can be up to 3 meters or longer, the nominal accuracy is 0.05% F·S, the accuracy of the sensor above 1 meter is 0.02% FS, and the repeatability is up to 0.002% F·S, so it is widely used.
By way of exercise
Linear displacement sensor
The function of the linear displacement sensor is to convert the linear mechanical displacement into an electrical signal. In order to achieve this effect, the variable resistance rail is usually fixed at the fixed part of the sensor, and different resistance values ​​are measured by the displacement of the slider on the slide rail. The sensor rail is connected to a steady-state DC voltage that allows a small current to flow through the microamperes, and the voltage between the slider and the start is proportional to the length of the slider movement. Using the sensor as a voltage divider minimizes the accuracy of the total resistance of the rail, as changes in resistance caused by temperature changes do not affect the measurement.
Angular displacement sensor
Angle Displacement Sensors are used in obstacle handling: using angle sensors to control your wheels can indirectly detect obstacles. The principle is very simple: if the motor angle sensor is configured to run and the gear does not turn, your machine has been blocked by obstacles. This technique is very simple to use and very effective; the only requirement is that the moving wheels cannot slip on the floor (or too many times), otherwise you will not be able to detect obstacles. This problem can be avoided by connecting an idling gear to the motor. This wheel is not driven by the motor but is driven by the movement of the device: if the idler stops during the rotation of the drive wheel, you are experiencing obstacles. .
According to the test material
Hall-type displacement sensor
Its measuring principle is to keep the excitation current of the Hall element (see the semiconductor magneto-sensitive element) constant and move it in a gradient-normal magnetic field, and the displacement is proportional to the Hall potential of the output. The larger the magnetic field gradient, the higher the sensitivity; the more uniform the gradient changes, the closer the relationship between the Hall potential and the displacement is linear. In Fig. 2, there are three kinds of magnetic systems that generate gradient magnetic fields: a system has a narrow linear range, and when the displacement Z=0, the Hall potential is ≠0; the b system has good linearity when Z<2 mm, when Z=0, Hall potential = 0; c system sensitivity is high, the measurement range is less than 1 mm. In the figure, N and S respectively indicate positive and negative magnetic poles. The Hall-type displacement sensor has a small inertia, high frequency response, reliable operation, and long life. Therefore, it is often used to convert various non-electric quantities into displacements and then perform measurement.
Photoelectric displacement sensor
It measures the displacement or geometry of an object based on how much light is blocked by the object being measured. It is characterized by non-contact measurement and continuous measurement. Photoelectric displacement sensors are commonly used to continuously measure wire diameter or as edge position sensors in strip edge position control systems.
Displacement sensor selection
The selection of the displacement sensor should meet the requirements of the following indicators:
1. Technical indicators of sensitivity
For an instrument, generally the higher the sensitivity, the better, because the more sensitive, the more easily the change of acceleration to the surrounding environment is felt, the acceleration changes greatly, naturally, the output voltage changes accordingly It becomes larger, so the measurement is easier and more convenient, and the measured data will be more accurate.
2, zero temperature
Zero point balance change caused by changes in ambient temperature. Generally, the change in the zero balance caused by the temperature change of 10 °C is expressed as a percentage of the rated output, that is, the drift of the input when the sensor is not pressed by the temperature change.
3. Technical indicators for bandwidth
Bandwidth refers to the effective frequency band that the sensor can measure. For example, a sensor with hundreds of HZ bandwidths can measure vibration, and a sensor with a bandwidth of fifty HZ can effectively measure the tilt angle.
4. Technical indicators of output mode
Digital output and analog output are two ways. The digital sensor inputs digital signals such as quantity and weight to the meter; analog sensors input analog signals such as voltage and current to the meter.
5. Technical indicators in terms of range
The range required to measure the movement of different things is different and should be measured according to the actual situation.
6, the ultimate overload
The maximum load that the sensor can withstand without losing its ability to work. This means that when the work exceeds this value, the sensor will be permanently damaged.
7, sensor gain
It is the original signal output magnification of the sensor.
Common faults and troubleshooting methods
The linear displacement sensor works on the same principle as a sliding rheostat. It is used as a voltage divider to present the actual position of the measured position with a relative output voltage.
1. If the electronic ruler has been used for a long time, and the seal has been aging, and there are many impurities, and the water mixture and oil will seriously affect the contact resistance of the brush, the number of the display will continue to jump. At this time, it can be said that the electronic scale of the linear displacement sensor has been damaged and needs to be replaced.
2. If the capacity of the power supply is small, there will be many situations: the movement of the glue will change the display of the clamped electronic ruler, there will be fluctuations, or the movement of the mold will cause the display of the electronic ruler to fluctuate, resulting in measurement error. Very big. If the driving power of the solenoid valve is at the same time when the power supply of the electronic scale is together, the above situation is more likely to occur. When the situation is serious, the voltage fluctuation of the multimeter can even measure the fluctuation of the voltage. If the situation is not caused by high frequency interference, static interference or neutral neutrality, then it may be caused by the power of the power supply being too small.
3. Both FM interference and electrostatic interference may cause the digital scale of the linear displacement sensor to jump. The signal line of the electronic ruler and the strong electric line of the device are separated from the wire slot. The electronic ruler must use the grounding bracket forcibly, and at the same time let the outer casing of the electronic ruler be in good contact with the ground. A shielded wire is required for the signal line, and a section of the electrical box should be grounded to the shielded wire. If there is high frequency interference, the voltage measurement using the multimeter will usually display normal, but the display number will be non-stop; when static interference occurs, the situation will be the same as high frequency interference.
To prove whether it is static interference, you can use a power cord to short the cover screw of the electronic ruler with some metal on the machine. As soon as it is shorted, the static interference will be eliminated immediately. of. However, if it is necessary to eliminate high-frequency interference, it is difficult to use the above method. Frequency conversion power savers and robots often have high-frequency interference, so you can try to verify whether it is high by stopping the high-frequency power saver or robot. Frequency interference.
4. If the electronic scale of the linear displacement sensor is in the process of working, the display data at a certain point is beating regularly, or when there is no data displayed, it is necessary to check whether the insulation of the connecting wire is damaged or not. And short circuit to ground caused by regular contact with the outer casing of the machine.
5, the voltage of the power supply must be stable, the industrial voltage needs to meet the stability of ± 0.1 [%], for example, if the reference voltage is 10V, it can allow fluctuations of ± 0.01V, if not, it will cause display The traps fluctuate like this. However, if the amplitude of the display fluctuation at this time does not exceed the fluctuation of the fluctuating voltage, then the electronic ruler is normal.
6. The alignment of the linear displacement sensor is very good, but the parallelism can allow an error of ±0.5mm, and the angle can allow an error of ±12°. However, if the parallelism error and the angle error are both too large, there will be a case where the digital jitter is displayed. Then, when such a situation occurs, the parallelism and angle must be adjusted.
7, in the process of connection, we must pay more attention to, the three lines of the electronic ruler can not be connected wrong, the power line and output line can not be exchanged. If the above line is wrong, there will be a large linearity error. It is difficult to control, the accuracy of the control will be poor, and the display will be prone to jitter.
There are many types of displacement sensors, and the application fields are expanding. At the same time, more and more innovative technologies are applied to sensors, such as OEM-based LVDT technology, ultrasonic technology, magnetostrictive technology, fiber optic technology, time grid technology, etc. Technology has made breakthroughs. Due to the advancement of technology, the performance of various sensors has been greatly improved, and the cost has been greatly reduced, thereby greatly expanding the application range and forming a high-speed growth industry.
ZGAR Disposable Vape
ZGAR Disposable Vape
ZGAR electronic cigarette uses high-tech R&D, food grade disposable pod device and high-quality raw material. All package designs are Original IP. Our designer team is from Hong Kong. We have very high requirements for product quality, flavors taste and packaging design. The E-liquid is imported, materials are food grade, and assembly plant is medical-grade dust-free workshops.
Our products include disposable e-cigarettes, rechargeable e-cigarettes, rechargreable disposable vape pen, and various of flavors of cigarette cartridges. From 600puffs to 5000puffs, ZGAR bar Disposable offer high-tech R&D, E-cigarette improves battery capacity, We offer various of flavors and support customization. And printing designs can be customized. We have our own professional team and competitive quotations for any OEM or ODM works.
We supply OEM rechargeable disposable vape pen,OEM disposable electronic cigarette,ODM disposable vape pen,ODM disposable electronic cigarette,OEM/ODM vape pen e-cigarette,OEM/ODM atomizer device.
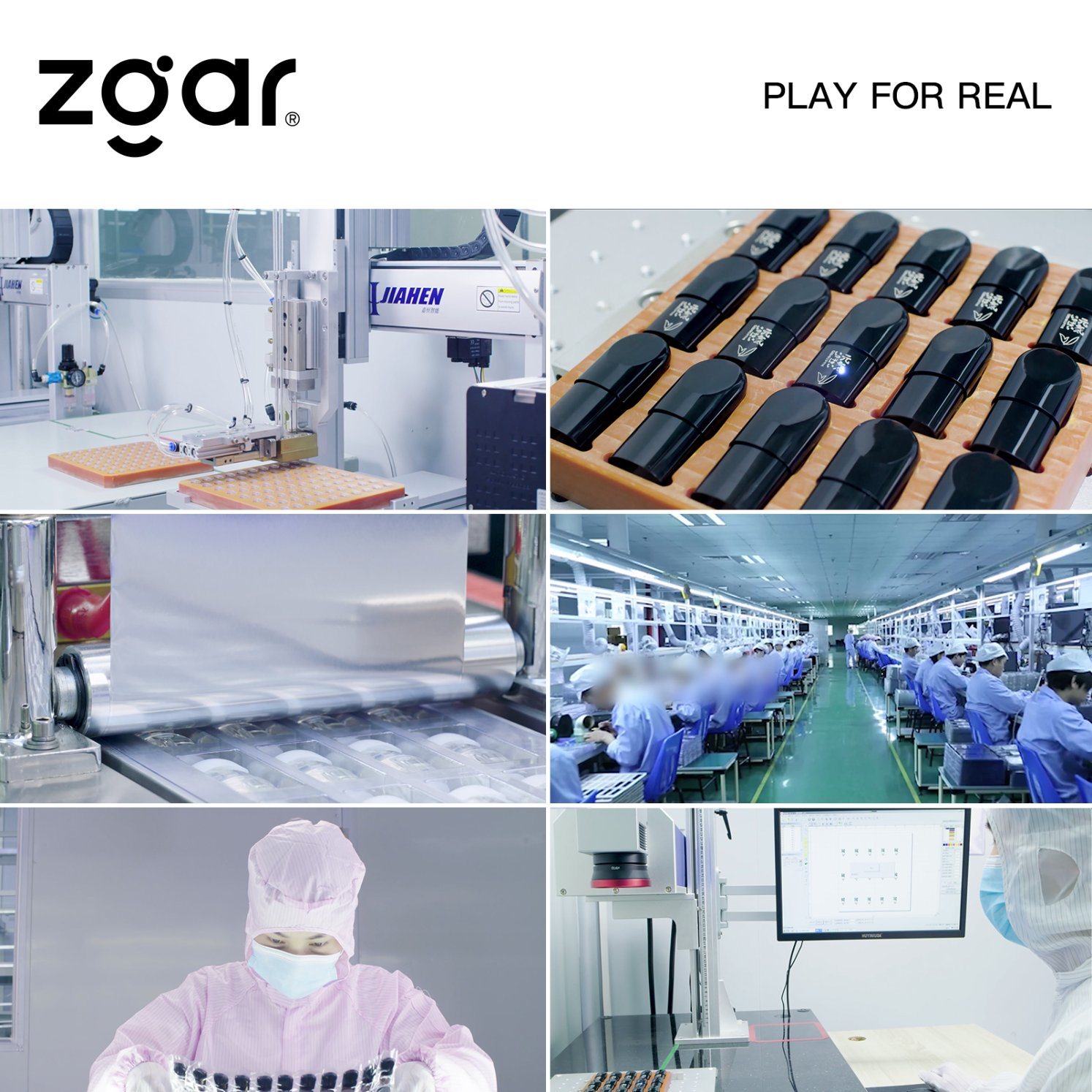
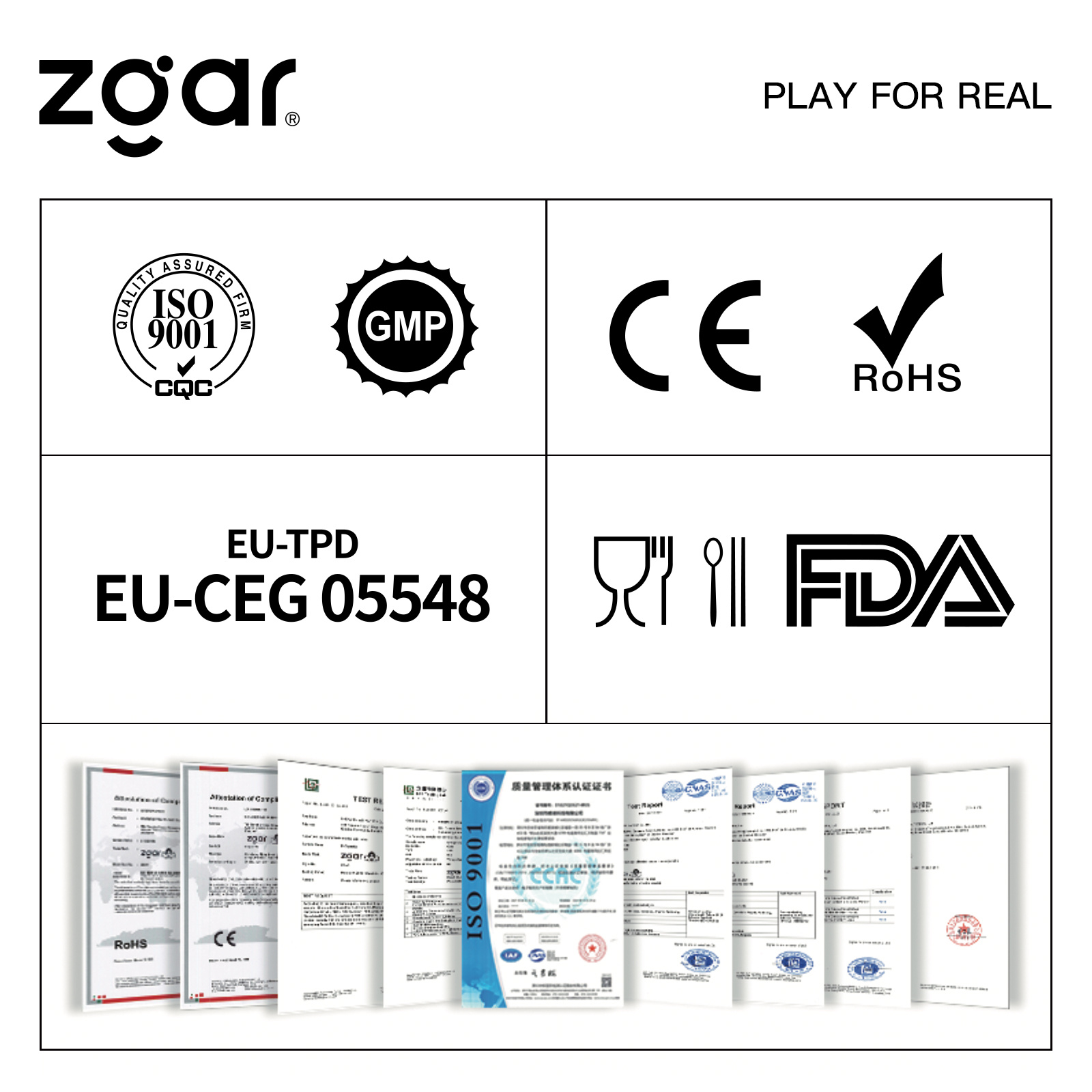
Disposable E-cigarette, ODM disposable electronic cigarette, vape pen atomizer , Device E-cig, OEM disposable electronic cigarette
ZGAR INTERNATIONAL(HK)CO., LIMITED , https://www.zgarette.com